
Sustainability and environmental awareness are becoming increasingly important. More and more companies are embracing the concept of circular design, which aims to make products resource-efficient so that they become part of a closed loop that minimises waste and pollution.
The Buoy Bottle is a prime example of circular design, with its sustainable production based entirely on solar energy and made from recycled plastic. The plastic used to make the bottles is collected from the oceans and rivers of Mexico and North America. Unlike other companies, Buoy does not use additives to make the plastic more flexible, so the shape of the bottle had to be adapted to the complex processing of the HDPE plastic. In addition, the bottles can be returned to Buoy at the end of their life to be recycled into new bottles. This creates a circular economy that reduces the carbon footprint by 80% compared to using virgin material.
The colourful drinking bottles can be combined in a variety of ways, as both the cap and the middle section of the bottle can be opened, for example to add ice cubes or make cleaning easier. Thanks to the optimised thread design, the cap can be opened with minimal effort, making the bottles ideal for active lifestyles.
The Red Dot Jury was impressed and honoured the Buoy Bottle with a Red Dot: Best of the Best:
“We think Buoy ticks all the boxes. Made from recycled ocean-bound plastic sourced from coastal regions in North America and elsewhere, it is a great example of a circular design product with impressive functionality. The surface is pleasant to the touch, and the bottles are easy to clean thanks to their modular design. The company even accepts them back for recycling at the end of their useful life. It’s the perfect closed cycle.“
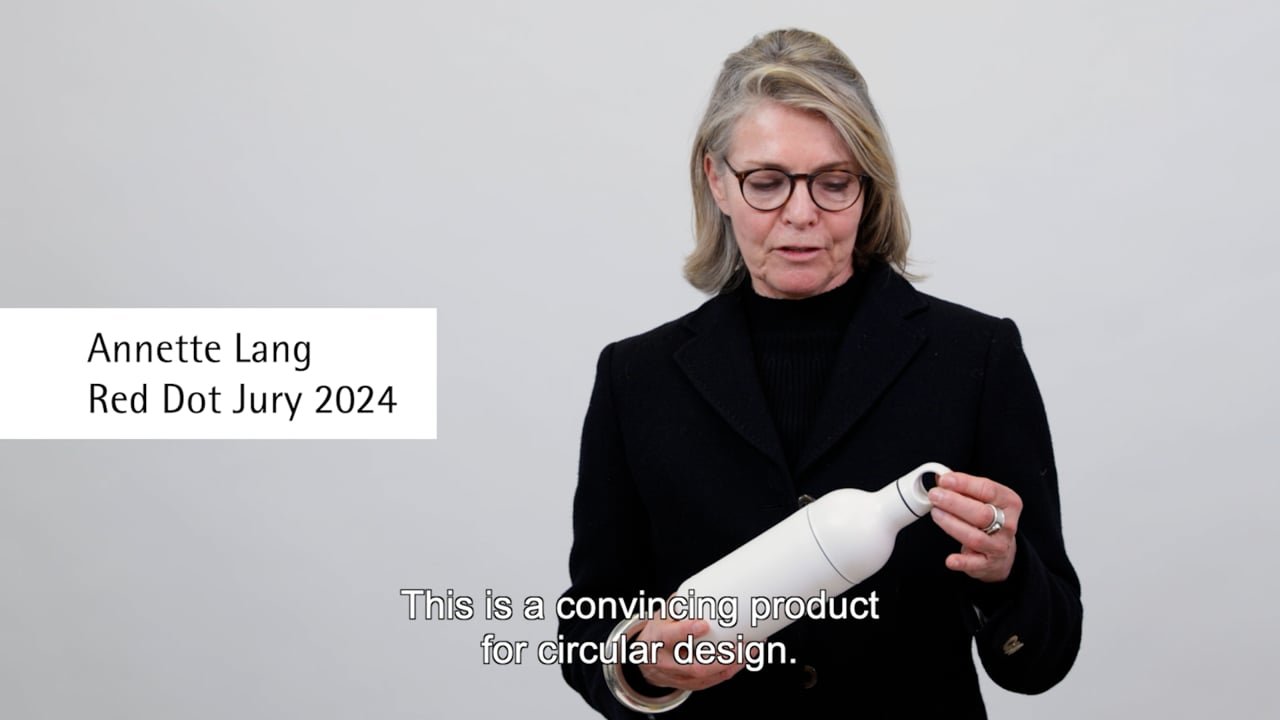
Interview with Pascal Schaller
Red Dot: Sustainable production was the focus of Buoy’s development. Can you tell us something about the material?
Pascal Schaller: We are very proud of the fact that we use 100 per cent recycled ocean-bound plastic. It is recovered from rivers and coastal regions in Mexico and California. We specifically source food-grade HDPE from recycled milk and juice bottles. A state-of-the-art recycling plant in Los Angeles processes these materials for us.
Are they easy to process or did you need innovative manufacturing techniques?
Using 100 per cent recycled material is anything but easy. Even the manufacturers encouraged us to add new plastic to improve the melt flow and to simplify production. But we refused. Four years, four manufacturers and two moulds later, we finally got the product right. You have to understand that recycled plastic without additives reduces the melt flow by a factor of 10, so we had to develop a mould for these specific conditions, with larger gates and a more complex cooling system to control the flow of material in the mould.
Which design detail was most important to you in Buoy?
The surface texture was a very conscious choice. We ensured that it was slightly rough for a secure grip, while at the same time providing a matt finish for the desired aesthetic. We also streamlined the bottle components to reduce weight and optimise durability, but also designed the thread to twist on and off with just a few turns for enhanced convenience.